“Dedicated Development Centre enables us to offer 360 degree design, development for toolings & prototyping solutions to our customers. This facility provides collaborative engineering support to customers to arrive at the best designs & prototypes faster.”
Ashok Iron Group’s Development Centre is first company in India offering integrated solutions since its inception from 1978. Our dedicated Development Center attained leadership status in design technology for Large Size / V-Type Engine Blocks, Engine Heads, Complex & Critical Castings and many more.
The team of specialist engineers specialized in areas like Gating/Risering Systems, Special Metallurgy, Lean Machining Set-ups work with manufacturing and quality teams to design, develop world class optimal processes. We use latest design software’s such as AutoCAD Mechanical & Invertor LT Suite for 2D Modelling, Unigraphics NX, Solid Edge, Pro E, for 3D modeling, Magma Soft for Metal Flow & Core Simulation & Unigraphics CAM NX, Master Cam & DNC Cimco for CAM.
Highlights:
- Simulation of Metal Flow and Core manufacturing.
- Design and manufacturing foundry toolings through CAD/CAM route.
- Design and manufacturing of Fixtures for castings & machining.
- Quality inspection through Flexible – Faro arm & White light scanning.
- Design of casting & machining process.


DEVELOPMENT PROCESS

In our drive of innovation, Rapid Proto Type Castings are developed via 3D Sand Printing Technology in place of long lead hard toolings and 5-Axis machining center for doing Machining with minimal machining toolings. With early engagement with customers in design phase and rapid prototyping the time to market products is drastically reduced. Added to it is the ease to manage the initial design changes in new products with lower cost.

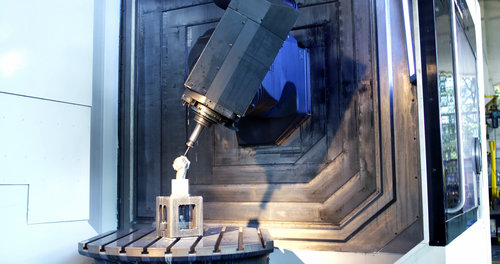
Deckel Maho – 5-Axis machine
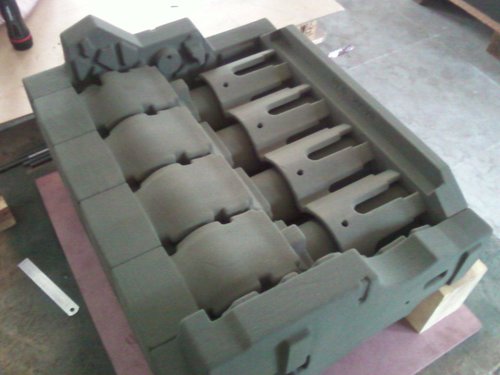
RAPID PROTOTYPING REQUIRMENTS
3D Printing Requirements | Advantages of Proto Making via 3D Sand Printing |
---|---|
3D CAD Model needed from Customer as a main input for to initiating activities for proto sample |
|
SOFTWARE’S WE USE




